Wenn Schiffe reden könnten, dann hätten sie was zu erzählen. Zum Beispiel, wie laut und wie gefährlich es gewesen sein muss auf der Helling der Stettiner Oderwerke AG im Jahr 1905. Da wurde nämlich ein knapp 16 Meter langer Schraubenschleppdampfer auf Kiel gelegt, der auch als Eisbrecher Dienst tun sollte und dieser Tage als „Ares“ in Mecklenburg unterwegs ist.
Die Stahlplatten des Rumpfes wurden damals nicht auf die Spanten (sozusagen das Gerippe des Schiffs) geschweißt, sondern genietet. So dicht wie möglich am Bauplatz stand seinerzeit ein mit Kohle beheizter Nietkocher. Der Nietheizer erwärmte die Nieten, bis sie rotglühend waren und warf sie dann mit einer Zange einem Kollegen zu, der fing den Niet in seinem Fangeimer auf, griff ihn mit der Zange und steckte ihn in ein vorbereitetes Loch. Innen im Rumpf stand dann der eigentliche Nieter der den Niet von Innen mit einem Presslufthammer und einem Hilfswerkzeug (dem Nietzieher) bearbeitete, so dass zwei Metallplatten pottendicht miteinander verbunden waren. Das stetige Hämmern auf Stahl muss eine enorme Geräuschkulisse ergeben haben.
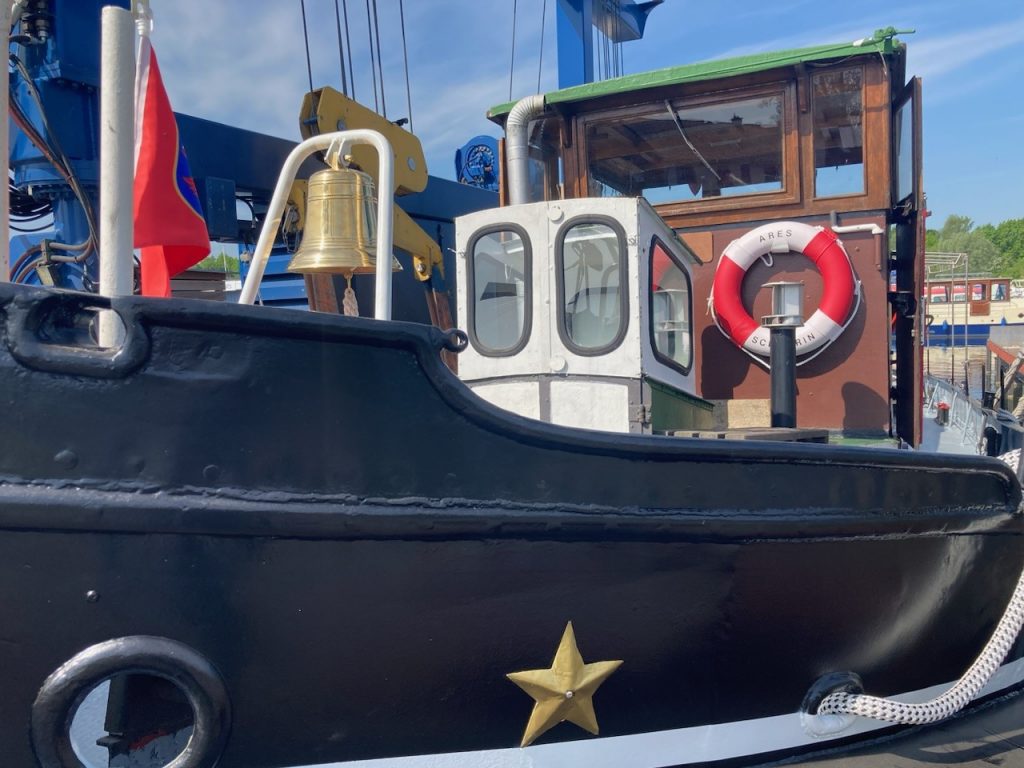
Die Eisennieten der „Ares“ sind stumme Zeugen dafür, mit welchem Aufwand und unter welchen Gefahren für die Arbeiter der Werft früher Schiffe gebaut wurden. Seit sich ab den 1940er Jahren das Schweißen im Schiffbau immer mehr durchsetzte, nimmt die Zahl der genieteten Schiffs- und Bootsrümpfe, die noch unterwegs sind, kontinuierlich ab. Selbst die dickste Stahlplatte hält dem Rostfraß nicht ewig stand. Umso ehrenwerter ist es, wenn ein solches Zeugnis der Schiffbaukunst erhalten wird.
Deck bemoost!
„Als ich die damalige ,Barbarossa’ und heutige ,ARES’ in Berlin zum ersten Mal sah, war klar, dass das in der ersten Zeit mehr Baustelle als Vergnügungsdampfer sein würde“, berichtet Astrid Hiersche und ergänzt: „Das Deck war im Bereich des Schanzkleids wie ein altes Hausdach teilweise mit Moos bewachsen. Teilweise konnte ich den Rost mit den Finger eindrücken.“ Der Plan war einfach: Der Schleppdampfer sollte auf eigenem Kiel und aus eigener Kraft von Berlin ins heimatliche Schwerin gelangen; und auf dem Weg dorthin sollte eine Werft angesteuert werden, die die „Ares“ aus dem Wasser heben, den Rumpf untersuchen und – wo erforderlich – instandsetzen konnte. Die Wahl auf die Kuhnle Werft.
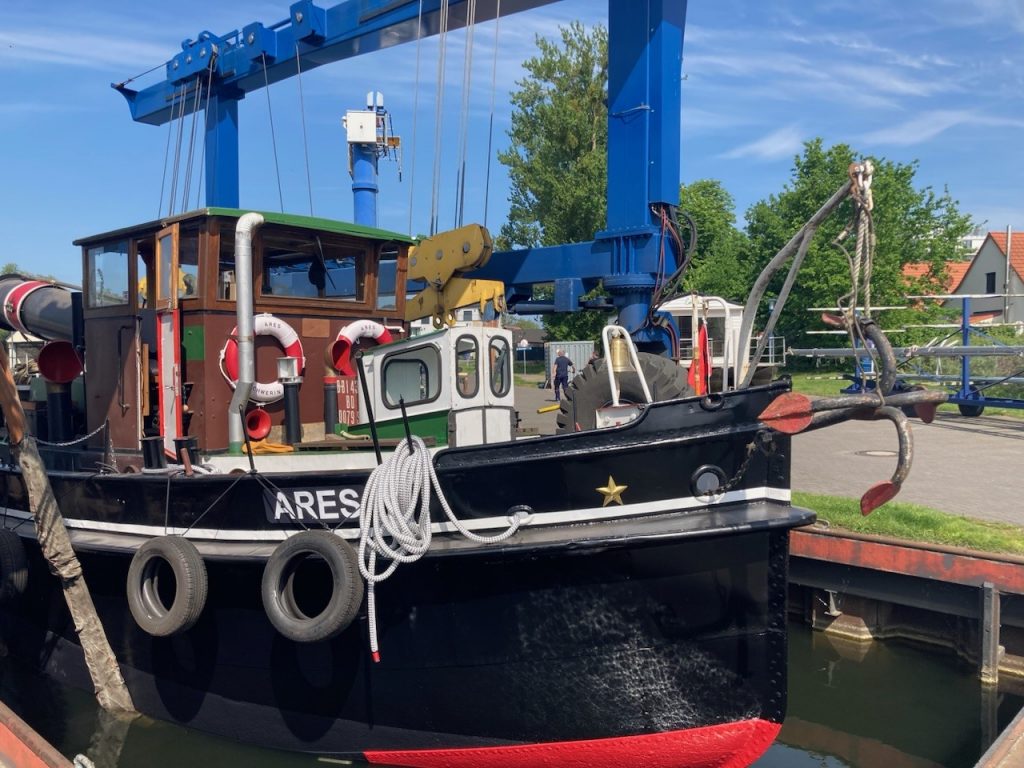
Die Arbeiten waren dann doch aufwändiger als erwartet. „Aber alles gut, mein Kundenbetreuer Christian Peter hat mich immer auf dem laufenden gehalten. Wir haben besprochen, was an weiteren Arbeiten notwendig ist und was das extra kosten würde. Und manche Stellen sieht man eben erst, wenn man die ersten Schichten Moos, Farbe und Rost abgetragen hat.“ Christian Peter und Franko Musfeld, der in der Werfthalle für die Ausführung der Arbeiten sorgte, hätten ihr immer transparent gemacht, was für ein Problem aufgetreten ist, wie die Lösung aussähe und was sie kosten würde. Vom Kranen, über die Schallmessung der Rumpfstärke, die Schweiß- und Lackierarbeiten am Unterwasserschiff, der Restaurierung der Ruderblattaufhängung, der Schweiß- und Lackierarbeiten auf dem Oberdeck, die neuen Opferanoden und der Erneuerung des Ankerkastens reichen die Werftarbeiten.
Boot zum Anpacken
Ganz ohne Schmerzen hat das neue Bauprojekt des Ehepaares Hiersche nicht begonnen. Schweren Herzens haben sie sich von ihrem letzten Restaurationsobjekt getrennt – einem neun Meter langen schwedischen Mahaghoniboot mit schlanken Linien und zeitloser Eleganz. „Ganz schwieriges Thema“ sagt Astrid Hiersche, die das Holz des verkauften Schweden restauriert, geschliffen, lackiert und wieder geschliffen und wieder lackiert hat. Frau Hiersche hat viel Liebe und Zeit in das Holzprojekt gesteckt und wird auch bei der „Ares“ wieder anpacken. Ihr Pro-Tipp für alle Frauen, die wie sie vor Dreckarbeit nicht zurückschrecken: „Fingernägel dick lackieren, dann sieht man die schwarzen Ränder nicht.“

„Mir war wichtig, dass die klassischen Werftarbeiten wirklich fertig sind“, sagt Hiersche. „Das was mein Mann und ich am im Wasser liegenden Schiff nicht selbst oder nur unter größtem Aufwand selbst machen können, wollte ich erledigt haben.“ Schließlich soll die „Ares“ die nächsten fünf Jahre im Wasser liegen bleiben. Da Hiersches Mann auch technischer Taucher ist, wird er den Rumpf zwischendurch eben im Wasser liegend vom Bewuchs befreien.
Sobald die „Ares“ an ihrem neuen Liegeplatz im Ziegelaußensee angekommen ist, geht für Hiersche und ihren Mann die Arbeit erst richtig los. Der Innenausbau steht an. „Es soll zeitgerecht sein, so auf dem Niveau der 20er oder 30er Jahre des 20. Jahrhunderts.“ Außer bei sicherheitsrelevanten Elementen (wie zum Beispiel einem Binnenfunkgerät) wird es keinen Kunststoff an Bord geben, statt Duschtasse gebe es dann eben eine verkupferte Zinkwanne.
Um den Antrieb macht sich Hiersches Ehemann wenig Sorgen. „Die originale Dampfmaschine ist schon 1978 ausgebaut worden, zwischenzeitlich war ein untermotorisierter Diesel installiert. Der ist in den 1990ern durch einen Daimler-Benz OM355-Diesel-Motor mit nun ca. 11,5 Litern Hubraum und immerhin 200 PS von 1969 ersetzt worden.“ Mit Schiffsdieseln kennt er sich als Diplom-Ingenieur für Schiffsbetriebstechnik aus. Bis auch der Motor perfekt in Schuss ist, wird das Schiff mit maximal 900 Umdrehungen gen Schwerin tuckern. Das bringt den 38 Tonnen schweren ehemaligen Schleppdampfer immerhin auf 10 Kilometer pro Stunde. Gleichwohl bleibt die Optik des Schiffs mit dem originalen, hohen klappbaren Schornstein erhalten. „Wenn man den nicht hätte niederlegen können, hättet ihr jetzt ein Oberlicht im Werftdach“, grinst die Eignerin der „ARES“. Dann schnappt sich das ambitionierte Ehepaar Pinsel und Farbrollen, der schwarze Rumpf muss noch den neuen Bootsnamen aufgemalt bekommen.